How CVC is Utilizing 3D Printing
CVC is officially “Certified Essential” with our partnership with Automation Alley’s Project DIAMOnD. With our new 3D printer, we are ready to address the COVID-19 pandemic when the urgent need for PPE and ventilators is in short supply. This partnership helps improve our region’s manufacturing agility and response to any future disruptions.
What is Project DIAMOnD?
“Project DIAMOnD is an initiative created by Automation Alley, Michigan’s Industry 4.0 knowledge center, that is dedicated to improving manufacturers’ agility and resiliency by helping them scale up their Industry 4.0 activity. More than 200 manufacturers have already received their printers and are ready to print personal protective equipment (PPE) when called upon to do so. In the meantime, they can also use the printers for creating parts critical to serving and growing their manufacturing operations.”
Read more: https://markforged.com/resources/news-events/markforged-project-diamond
What advantage does 3D printing bring to CVC?
The 3D printer’s biggest strength has been aiding in custom fixtures out on the manufacturing floor, specifically for laser engraving and assembly. These prints are lightweight, repeatable, produced quickly with minimal labor, and can potentially exceed the functionality of traditionally made parts in certain applications. This ultimately makes the manufacturing and assembly process simpler and more reliable, while reducing cycle times, and increasing customization regarding safety and ergonomics.
We have also printed one “surrogate” for a new part. This allowed the machinists to utilize the 3D print in setting up their machines and programs. It is extremely beneficial to have a physical reference in addition to the provided dimensional drawings.
What does the future look like for CVC and 3D printing?
The future is looking bright for CVC’s additive manufacturing potential. Upcoming considerations for research and development, are as follows:
- Surrogate Parts
- Testing fixtures or jigs in advance with a print, ahead of final production parts.
- Soft Jaw Inserts for Vices
- This aids in holding more complex parts by customizing inserts to match the unique geometry of a specific part.
- Grips for Robotic Applications
- This will aid in the automation process that encounters the final product. These grips are usually custom designed to match the parts geometry.
- Go/No Go Gauges
- Features that cannot be easily or quickly verified using traditional measuring methods and can instead be printed in the form of a custom template.
- CMM Fixtures
- Holding parts that have complex profiles in position.
- Assembly/Disassembly Jigs
- Aiding in reducing cycle times and improving consistency across all custom subassemblies. In certain applications, this process tends to be the most labor-intensive part of the manufacturing process.
- Low-force Templates
- Aiding in something as simple as applying labels or markings in the same exact location on final products.
- Storage and Organization
- Printed material outlasts any foam inserts used for custom part storage.
This project not only provides an avenue for Custom Valve Concepts to utilize its abilities to help those in our community but has also helped kickstart our goal of introducing additive manufacturing into the company!
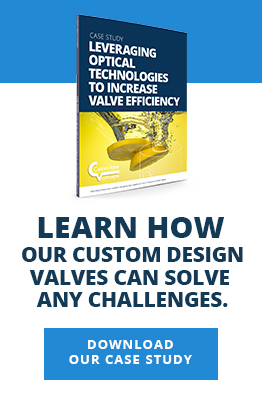
Sign up to receive the CVC Engineering Insights in Your Inbox:
Join us on Social Media!





Learn more about Custom Valve Concepts
Blog categories
- mechanical design (7)
- General (15)
- history (1)
- quality (4)
- manufacturing (4)
- meet the team (4)
- FAQ Kates (3)